Additive manufacturing provides a more efficient and customizable alternative to traditional manufacturing methods, allowing for complex designs with ease and precision.
While all 3D printing is additive manufacturing, not all use the 3D printing process. This distinction opens the door to various techniques that can be used with different materials and applications.
Overall, this manufacturing enables a reduction in material waste, increased design flexibility, and tailored products to meet individual needs.
A thorough answer to what is additive manufacturing will be found in this article. I went through intense research to teach you about additive manufacturing, including its history, technologies, and materials. Discover its benefits and challenges, and see how it’s transforming manufacturing.
Key Takeaways
- It builds objects layer by layer, allowing for complex, customized designs.
- It includes a range of techniques beyond 3D printing, each with specific applications and materials.
- It offers significant advantages over traditional manufacturing, including efficiency and design flexibility.
Here are the sections we will explore:
What Is The Additive Manufacturing Process?
Key Technologies and Techniques
Grasping the Basic Principles
History of Additive Manufacturing
From Conception to Modern Day
Notable AM Products and Projects
Materials Used in Additive Manufacturing
Applications of Additive Manufacturing
The 7 Types of Additive Manufacturing
Advantages and Challenges of Additive Manufacturing
FAQ
What Is Additive Manufacturing: Understanding the Process
Ever wondered how you can turn a digital file into a complex physical object? Well, that’s the magic of additive manufacturing (AM), also known as 3D printing. It’s like making a cake, but you’re layering materials instead of flour and eggs. Let’s dive in!
The process starts with a digital design. Imagine using your computer to create a virtual blueprint of what you want to make. This design is often crafted in CAD (Computer-Aided Design) software.
Materials come next. Depending on the AM technique, this could be a resin, metal powder, or plastic filament—think of the different ingredients you could use in a recipe.
We’ll dive into the various types of techniques later.
The intricacies of materials science are crucial here, as each method affects material properties differently. Adjust the process like you tweak recipe components for the perfect texture and taste.
With AM, you go from digital to physical in a cleaner, more precise way than traditional means. As you build up layer by layer, you’re conserving material just like you would by not over-pouring batter. That’s efficiency with a touch of artistry!
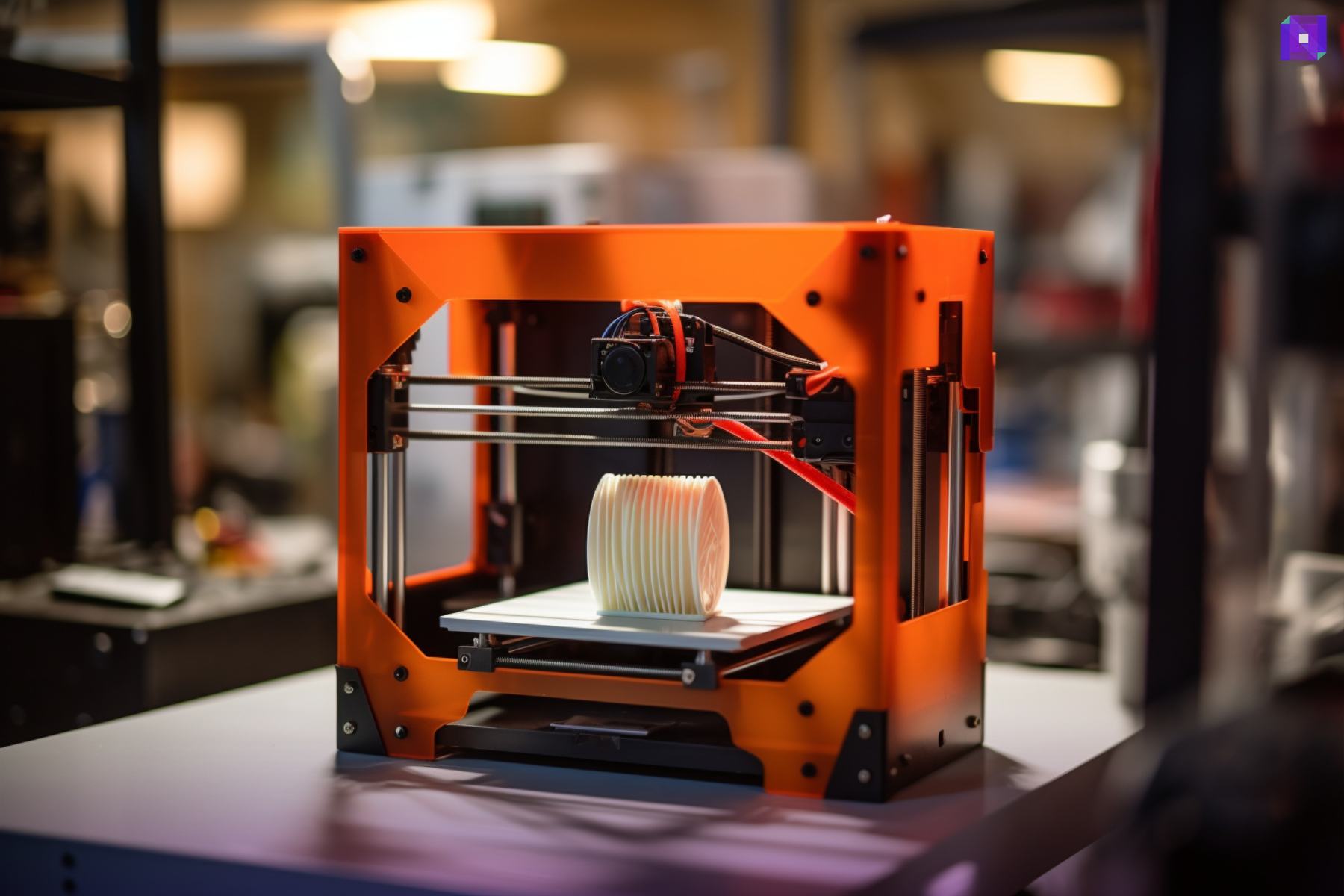
Key Technologies and Techniques
At the heart of AM there are several core technologies. Fused Deposition Modeling (FDM) is like using a hot glue gun but much more precise and controlled. The material is melted and extruded through a nozzle to build your design. Affordable FDM printers are a hit with hobbyists and professionals alike.
Moving on to something more high-tech, Selective Laser Sintering (SLS) machines use powerful lasers to fuse plastic, metal, glass, or ceramic particles. It’s like making sandcastles with laser beams! And because no supports are needed during printing, your SLS creations can have complex geometries that are challenging (or nearly impossible) to achieve with traditional manufacturing.
Common AM Technologies | Description |
FDM | Melts material and extrudes it, adding layers |
SLS | Uses lasers to sinter powdered material |
SLA | Cures liquid resin into solid with UV light |
Now, let’s talk shop! In the software world that brings your 3D models to life, Autodesk Fusion 360 is a superstar, offering a robust suite of design, engineering, and simulation tools. Fancy something more user-friendly? Cura has your back—it slices your digital 3D model into layers and calculates precisely how your printer will build it.
Each AM technology has its own superpowers, and picking the right one depends on what you’re creating. Whether you’re whipping up a prototype or crafting end-use parts, there’s a technique for you. Just remember: the future of making things is literally at your fingertips.
Grasping the Basic Principles
First things first, you need a design. This isn’t your ordinary sketch on a napkin; you’ll use computer-aided design (CAD) software or capture the nitty-gritty with a 3D scanner. Once your masterpiece is digital, it’s time to get it AM-ready by converting it to a particular file format like STL or AMF. Think of this step as teaching your AM machine to speak the same language as your design.
Next up, slice and dice—metaphorically, of course. Your design is split into thin, horizontal layers. It’s like slicing a loaf of bread but in reverse. This slicing is critical because it’s the roadmap for your AM machine, laying out the exact path it needs to follow.
Choosing the right material is critical. You could go classic with plastic or avant-garde with metal or even ceramics. It’s like picking the perfect outfit; it has to suit the occasion—depending on what you’re making.
Now, the real magic begins. Your AM machine adds these materials layer by layer, adhering to the software’s precise instructions. Slowly but surely, your idea comes to life, each layer fusing with the last.
When the printing show is over, it still needs to be finished. Time for some post-production jazz! Clean off any excess material because who likes rough edges, right? Some objects need a little spa treatment: a heat bath, a polish, or a fancy coating. And voilà, your object is ready to go from the digital world to reality!
History of Additive Manufacturing
Did you know that the journey of additive manufacturing (AM) started over three decades ago?
Back in the 1980s, a man named Charles “Chuck” Hull filed the first patent for a method known as stereolithography. This was a groundbreaking approach, where solid objects were created from digital data by printing successive layers of material. Imagine the excitement of seeing something drawn on a screen come to life!
Important Milestones:
- 1981: Hideo Kodama of the Nagoya Municipal Industrial Research Institute makes strides in AM but doesn’t file a patent.
- 1984: Chuck Hull invents stereolithography, files for a patent, and co-founds 3D Systems Corporation.
- 1980s: AM is primarily used for rapid prototyping, not creating functional parts.
Years before Hull’s patent, a visionary named Johannes F Gottwald filed a patent apparatus for the layered buildup of models in 1979. While not as widely recognized, this work laid some foundational ideas for what was to come.
Did you realize that even before the ’80s, science fiction had a say in this? A story called “Things Pass By” by Murray Leinster in 1945 described a form of 3D printing. Some would say he saw the future before most of us!
In publishing, the term “additive manufacturing” was coined much later and detailed in peer-reviewed journals, solidifying its place in manufacturing lexicons. Even now, AM continues to evolve, and copyright issues are hot topics as digital files for 3D printing can spread rapidly across the internet.
From Conception to Modern Day
As mentioned, it started in 1983 when Chuck Hull invented stereolithography (SLA). Then, the late ’80s saw a burst of creativity:
- 1983: Chuck Hull prints the first 3D part, a small cup, using SLA.
- 1987: Hull’s company, 3D Systems, introduces the SLA-1, the first commercial AM machine.
- 1988: Fused Deposition Modeling (FDM) is developed by Scott Crump.
- 1989: Selective Laser Sintering (SLS) emerges, thanks to Carl Deckard.
- 1990: Michael Feygin brings us Laminated Object Manufacturing (LOM).
Jump to 2005, and the RepRap project kicks off, paving the way for homebrew tinkering with 3D printing—no big factory required. Fast forward to 2009, and the MakerBot is on the scene, bringing AM into garages and workshops worldwide!
And as for applications of this amazing tech? It makes waves in aerospace, healthcare, jewelry, and fashion.
Key advancements didn’t stop there:
- Metal AM
- Multi-material printing
- Bioprinting
- Nanoscale AM
- 4D printing
With each leap, AM has crept closer to your daily life. It’s not just for prototypes. We’re talking end-use parts and unimaginable complexity. Neat, right?
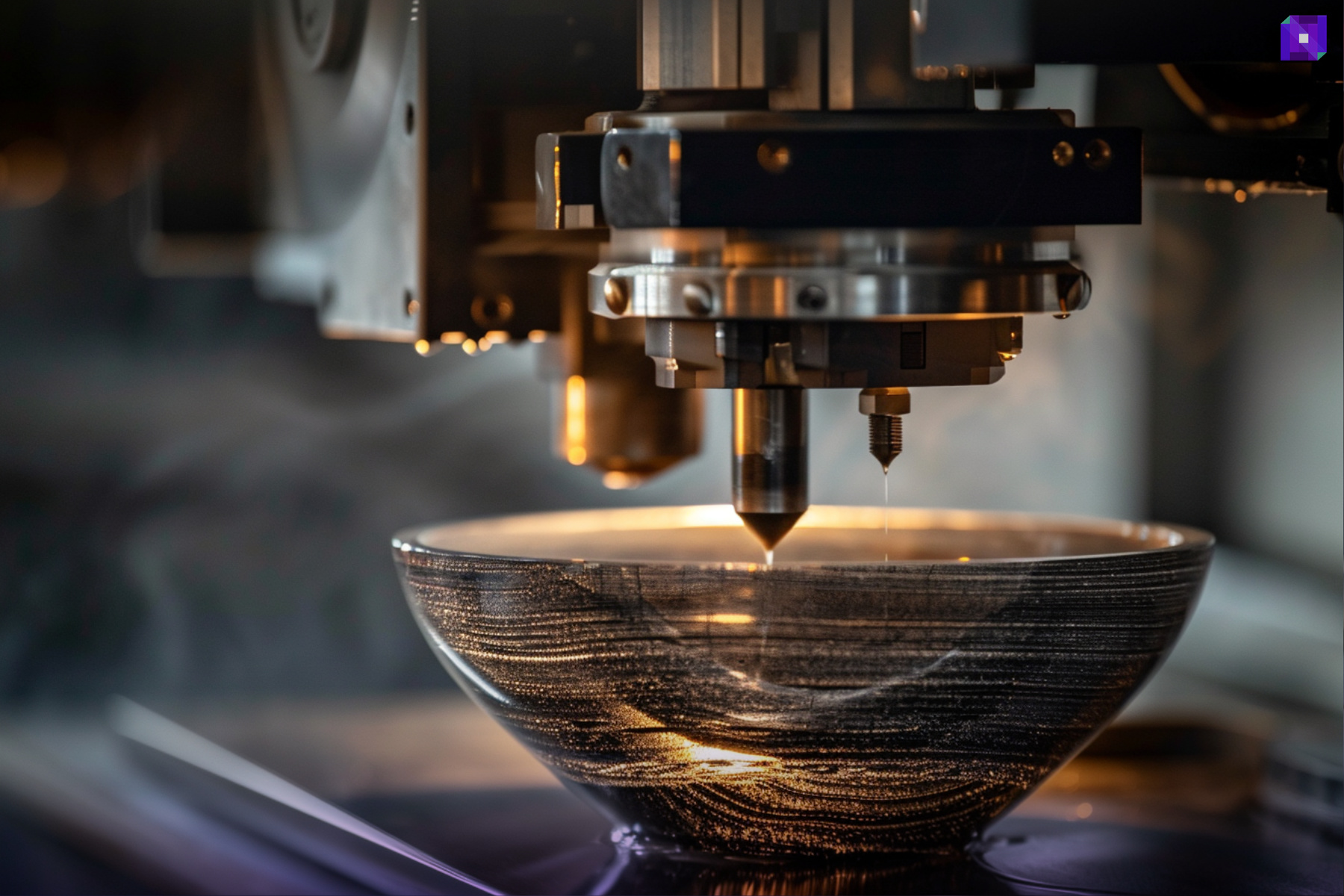
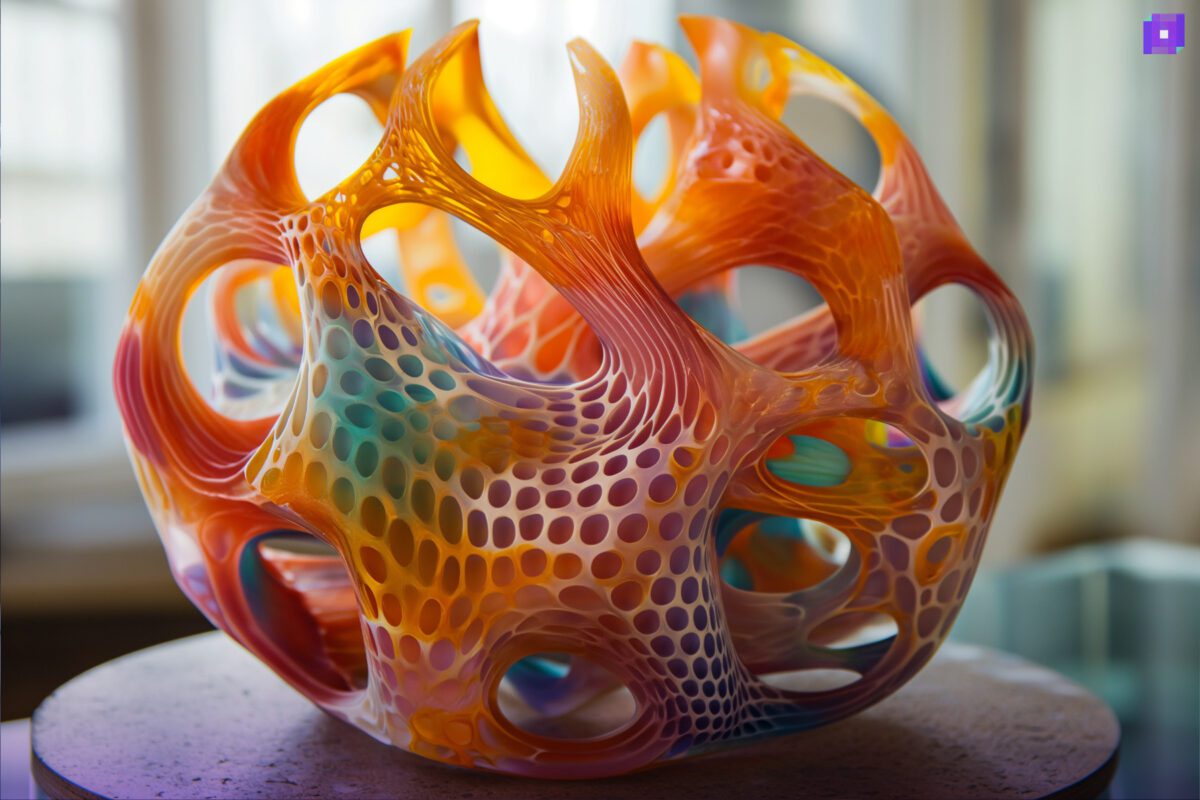
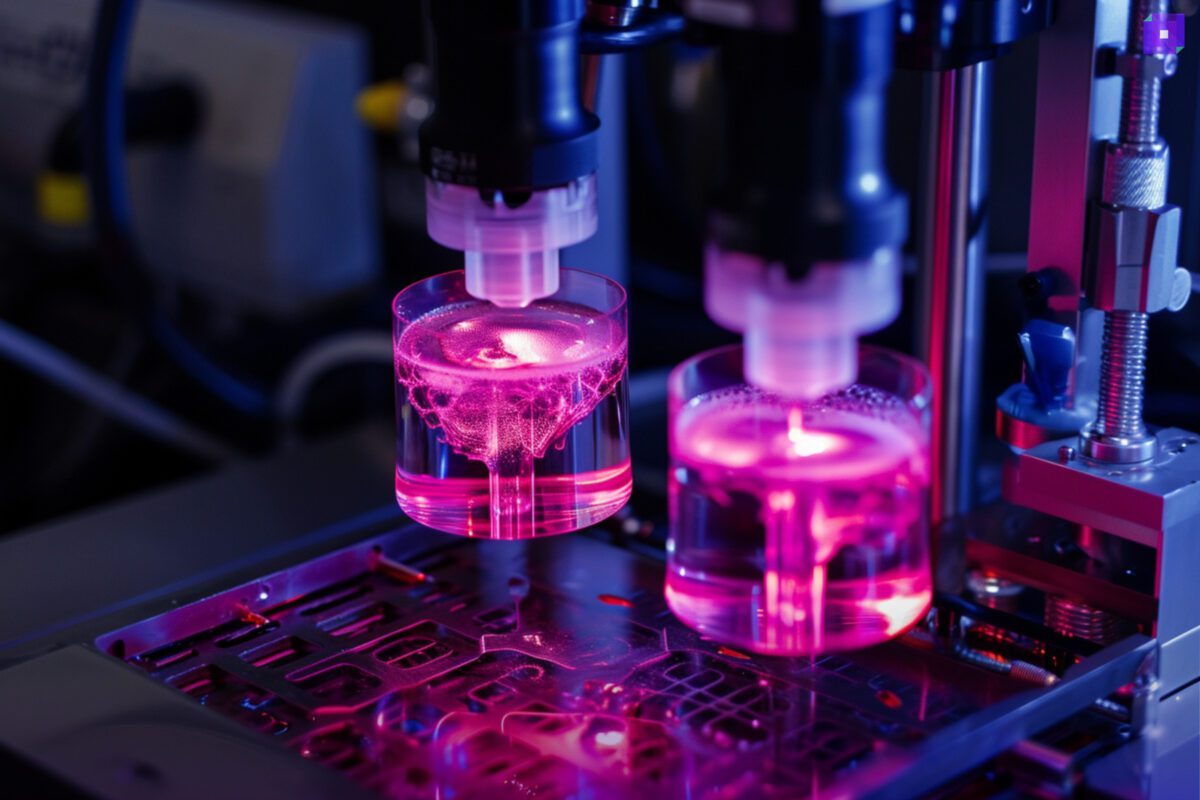
Notable AM Products and Projects
Here’s a snapshot of groundbreaking AM projects and products:
- The Pioneer in Medical Miracles: Imagine needing a new organ and simply printing it out. It sounds like science fiction, right? Yet, back in 1999, the first 3D-printed organ, a bladder, was given to a grateful patient. Dr. Anthony Atala’s work paved the way for future medical marvels.
- The Green Machine on Wheels: In 2011, the world got its first peek at the Urbee, the first 3D-printed car by Kor Ecologic. This wasn’t just any car; it aimed to be as environmentally friendly as possible and set a new green standard for the automotive industry.
- The Debate Trigger: Enter 2013, and Cody Wilson introduced the Liberator—the first 3D-printed gun. It sparked conversations around the globe on the implications of such accessible manufacturing.
- A Constructive Leap: By 2016, Dubai said “Hello” to an architectural wonder—the Office of the Future. This was the first 3D-printed building, showcasing that homes and offices could rise from a bed of powder and binders.
- Blast Off with Precision: 2017 witnessed the Rutherford rocket engine by Rocket Lab, elegantly crafted through 3D printing, demonstrating that even the sky isn’t the limit for AM.
Each project exemplifies how AM reshapes our world, from healing, riding, and protecting to exploring the cosmos. They are not just notable — they’re landmarks etched in the timeline of manufacturing innovation. And guess what? You’re living in this era of incredible creativity!
Materials Used in Additive Manufacturing
Ever wondered what goes into printing a three-dimensional object? It’s not just plastic! AM or as you know it, 3D printing, employs a diverse array of materials, each with unique properties that make your designs come to life.
From metals to polymers and ceramics to composites, the choice of material depends on the intended use of the final product. Do you have a part that needs to withstand extreme heat? Metals are your best bet. Looking for something with a bit of flexibility? Polymers like resins or gels could be the answer.
Different AM techniques also influence the material selection. For instance, Powder Bed Fusion is perfect for metals and ceramics, using a laser to sinter powder particles into a dense and strong object.
Material Type | Properties | Common Uses |
Metals | Strong, durable | Functional parts, tooling |
Polymers | Flexible, lightweight | Prototyping, consumer products |
Ceramics | Heat resistant, hard | Medical devices, aerospace components |
Gels & Foams | Soft, compressible | Cushioning, biomedical applications |
In the AM realm, polymer composites and blends broaden the material properties spectrum, offering strength and design flexibility. Whether it’s the resins used in stereolithography or foams for soft structures, these materials can really amp up your project.
Material properties are paramount in AM, as they dictate your final piece’s durability, flexibility, and heat tolerance.
Plastics
Have you ever marveled at the intricate details of plastic toys or how quickly a prototype can come to life? It’s all thanks to 3D printing with plastics. Plastics are incredibly versatile for 3D printing, accommodating a variety of forms like filaments, powders, pellets, or even liquids. Let’s dive into some commonly used plastics in this innovative process:
- ABS (Acrylonitrile Butadiene Styrene): It’s rigid yet flexible and durable.
- PLA (Polylactic Acid): Eco-friendly and biodegradable, it’s a hit for conscious creation.
- Nylon: Known for its strength and flexibility.
- PET (Polyethylene Terephthalate): Common in your water bottles, PET is recyclable and food-safe.
- Photopolymers: These liquids harden under light, perfect for precise details.
Mainly, PLA is a star in FDM (Fused Deposition Modeling) printing. Imagine you’re crafting low-cost, environmentally friendly items. Use PLA to churn out fun toys, accurate models, or functional prototypes without hurting the planet.
Example Usage of PLA:
- Toys: Safe for the little ones and good for the earth.
- Models: Ideal for your architectural dreams or hobbyist desires.
- Prototypes: Kickstart your invention with a minimal carbon footprint.
So, why should you care? Using plastics opens a realm of possibilities. You can quickly bring your ideas into the physical realm, test concepts without heavy investments, and even personalize them to your heart’s content. And doing all that while staying eco-conscious? That’s just brilliant!
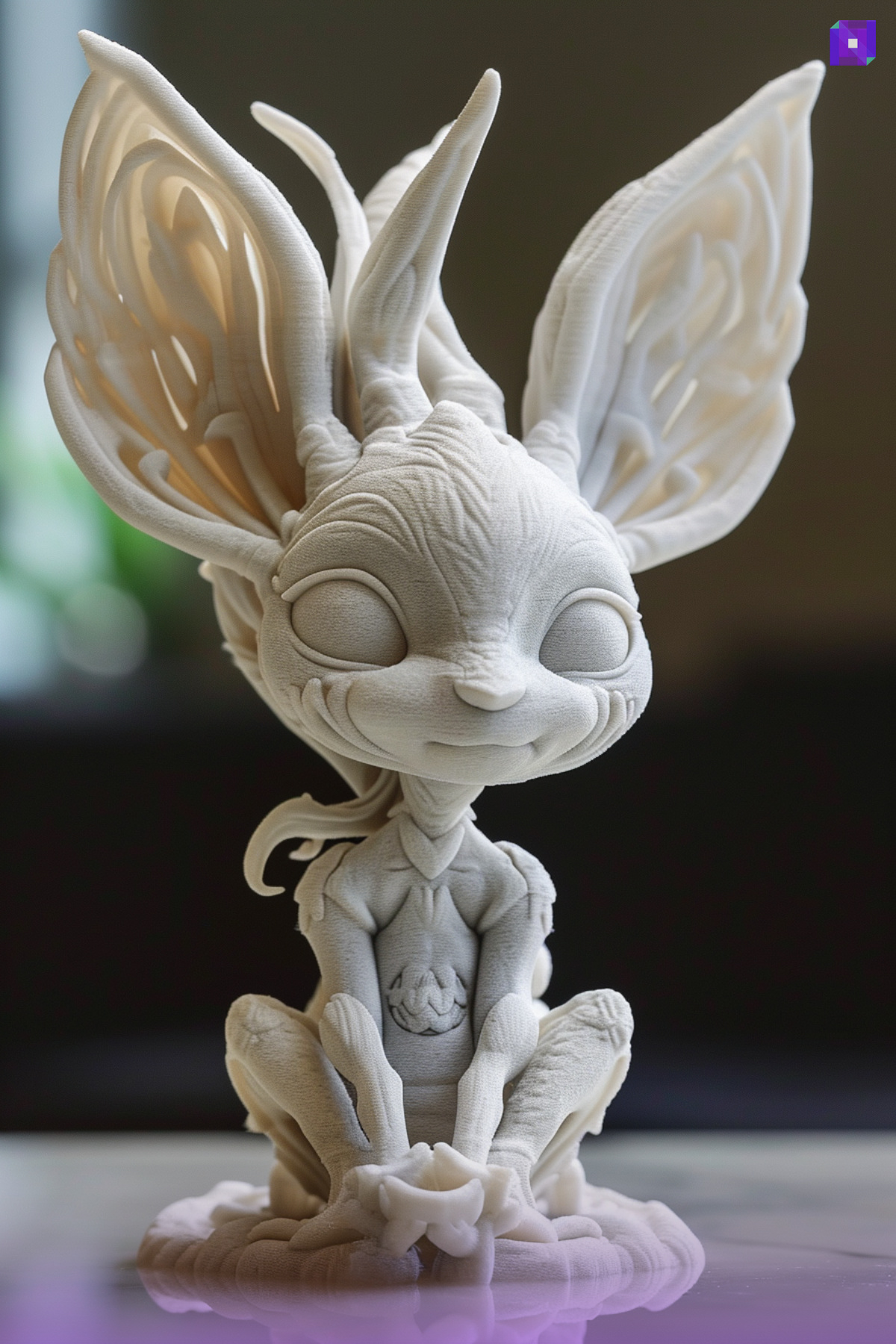
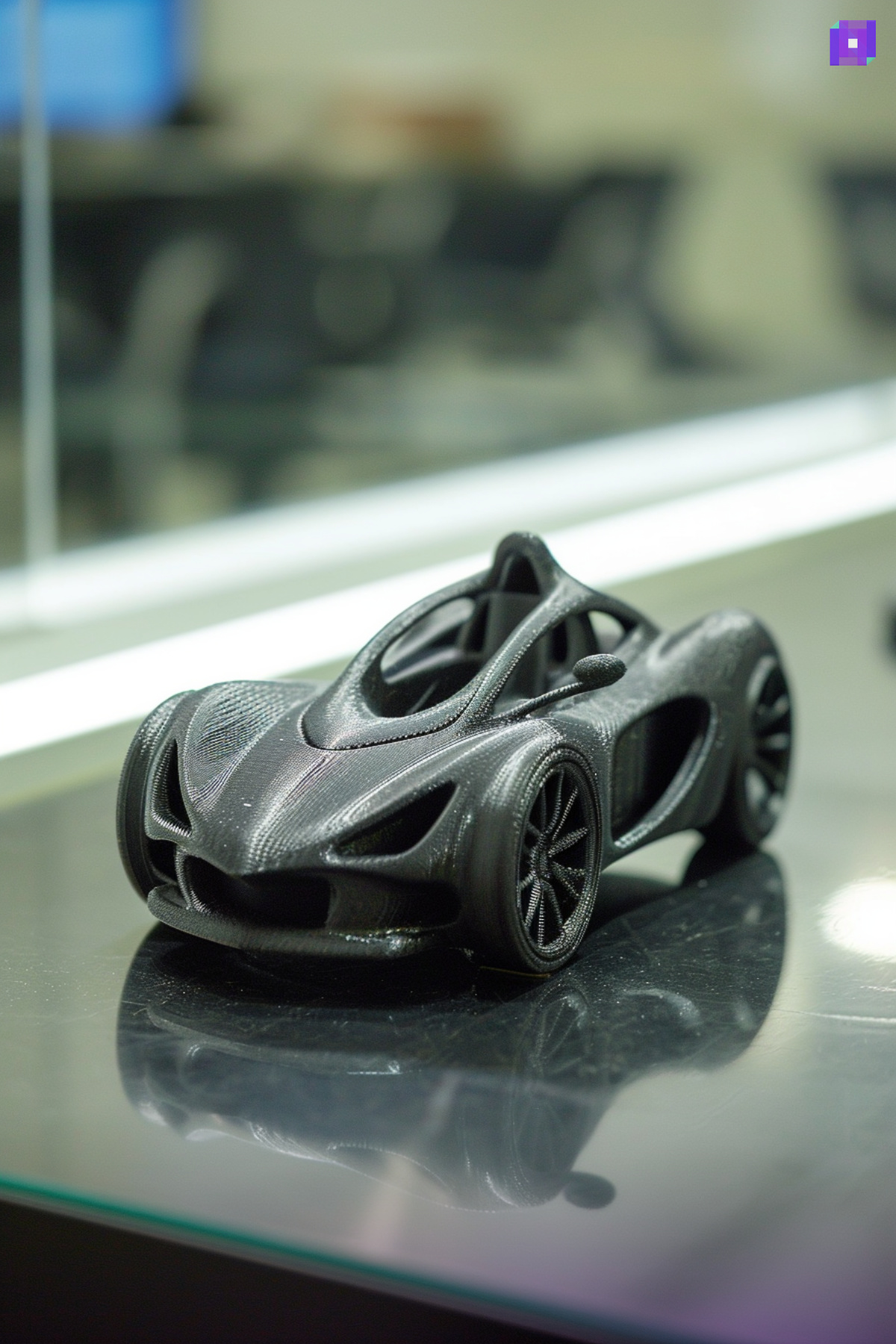
Metals
Have you ever wondered what makes some materials perfect for high-flying jets or life-saving medical devices? Well, the secret often lies in the metals used in additive manufacturing. Not just any metals, we’re talking about the solid and durable champs of the material world. These are not your everyday tin foil and soda can metals, but titanium, aluminum, steel, copper, and even gold!
Titanium, for instance, is a real superhero in the world of metals. It’s robust and doesn’t corrode, which means it’s fabulous for making things like medical implants and prosthetics with Selective Laser Sintering (SLS) or Direct Energy Deposition (DED). Picture yourself with a jaw made of the same stuff as a fighter jet – pretty cool, right?
Metals like these have opened up new horizons in industries that demand the best of the best. Think aerospace, automotive, or medical fields—areas where failure isn’t an option.
Metal | Properties | Common Uses |
Titanium | Lightweight, corrosion-resistant | Aircraft components, implants, prosthetics |
Aluminum | Durable, light | Automotive parts, aerospace frames |
Steel | Strong, versatile | Structural components, machinery |
Copper | Conductive, antibacterial | Electrical components, antimicrobial surfaces |
Gold | Ductile, non-reactive | Electronics, dental applications |
Remember, each of these mighty metals plays its own unique role in pushing the boundaries of what we can create. They offer an array of qualities that can be harnessed for cutting-edge applications. The next time you zoom down the freeway or board a jet, think about the wonders these metals do when layered up, bit by bit, to support how we live and work!
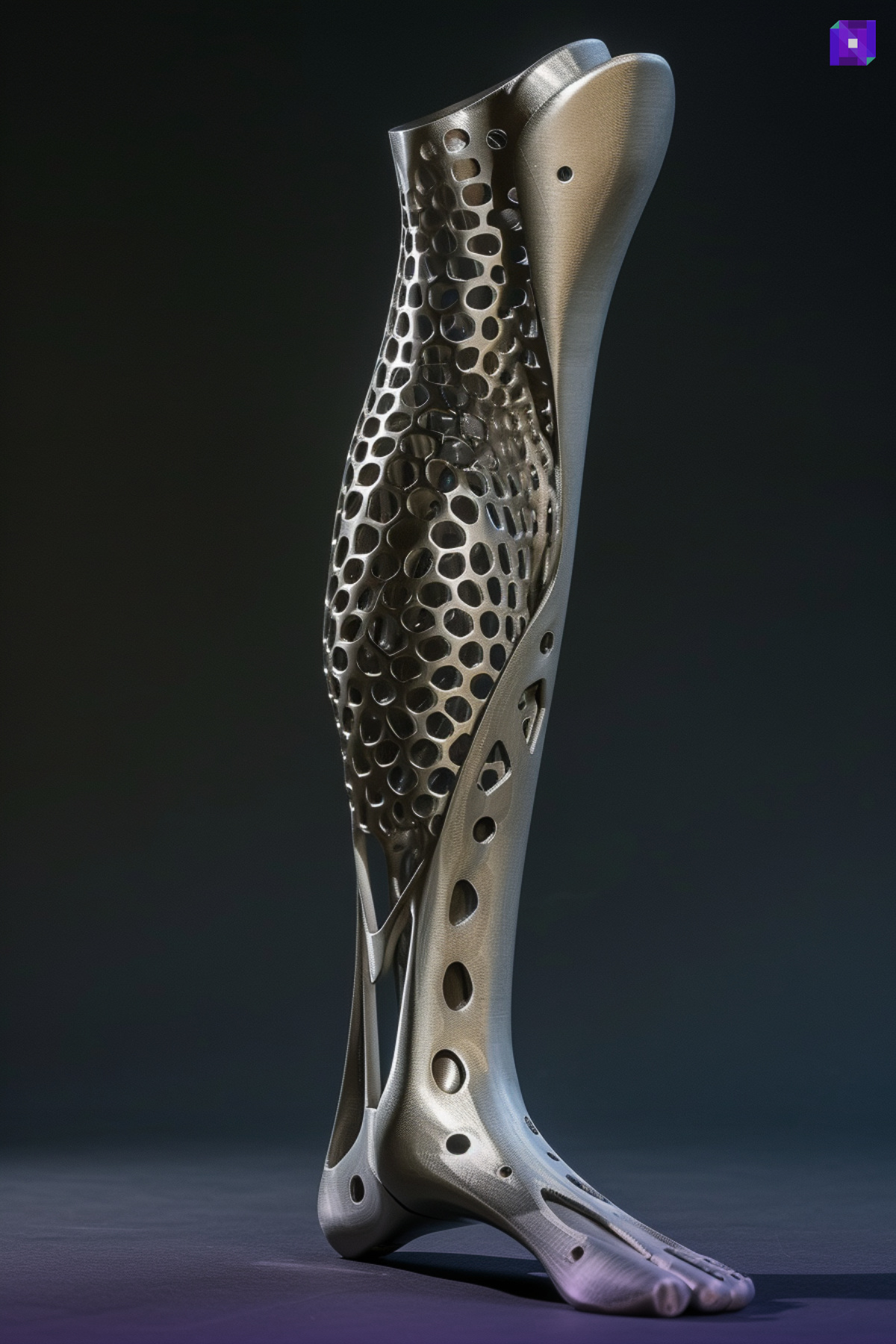
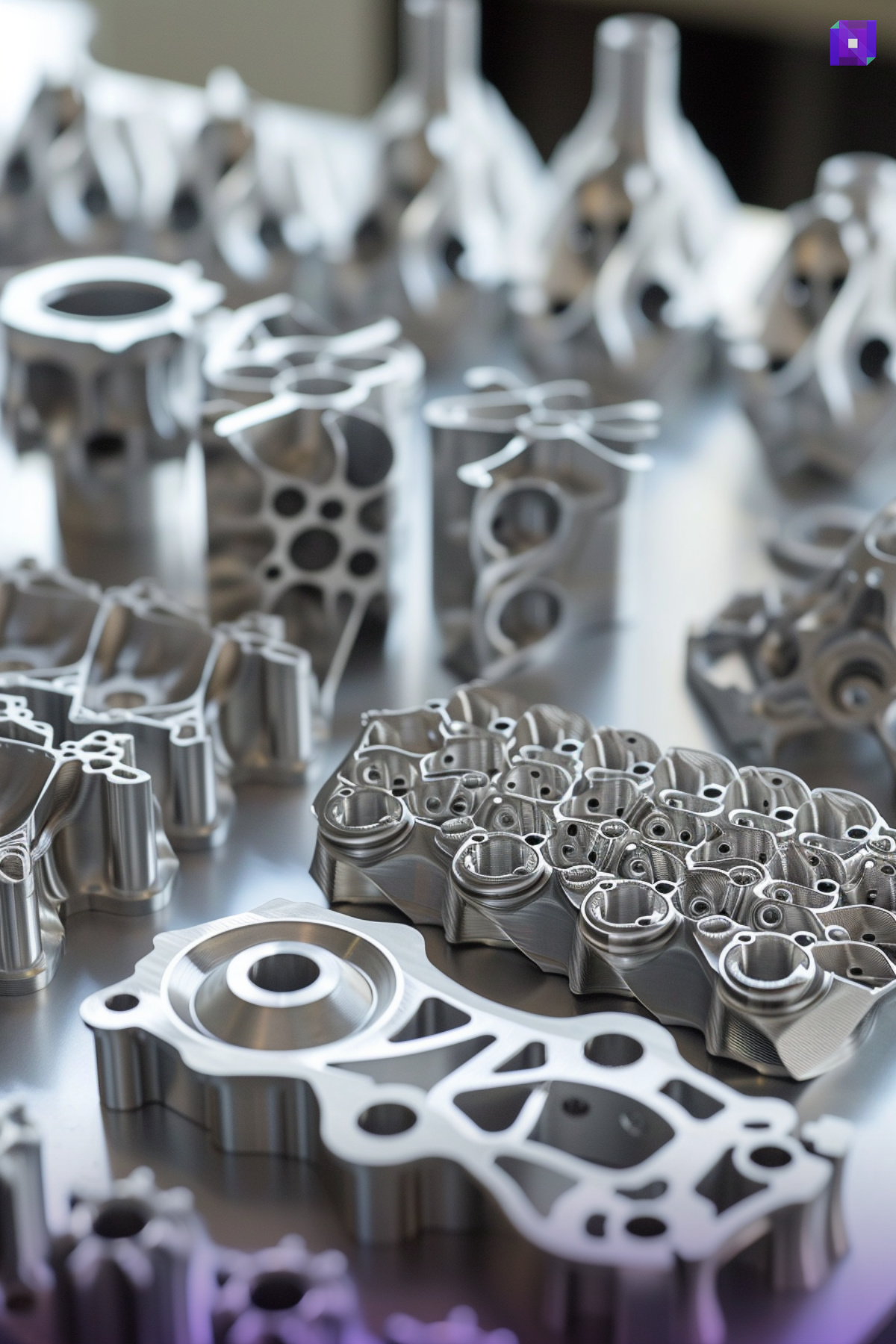
Polymers
Let’s chat about polymers, those versatile materials making waves in the industry.
In 3D printing, polymers are like the all-rounders, ready for anything you throw at them. Thanks to their adaptability and wide range, they’re the go-to for many applications. Abundant and diverse, polymers come in flavors like PLA, ABS, and nylon, each bringing its own perks to the table. For instance, PLA is beloved for being biodegradable, making it a hit with the eco-conscious crowd.
Curious about tailored performance? Enter composite materials. Imagine mixing chocolate chips into your cookie dough – that’s what we’re doing here but with materials. Composite polymers, like carbon fiber infused filaments, increase strength and stiffness. Picture a fancy carbon fiber bike frame or a sleek helmet crafted through material extrusion or material jetting—strong, right?
For the fans of detail and finish, photopolymers bask in the spotlight. They’re perfect for Stereolithography (SLA) or Digital Light Processing (DLP). Need a smooth, detailed object? A shiny new piece of jewelry or a dental crown that fits just right? Photopolymers are your best bet. They solidify under light to give you that crisp detail and polish.
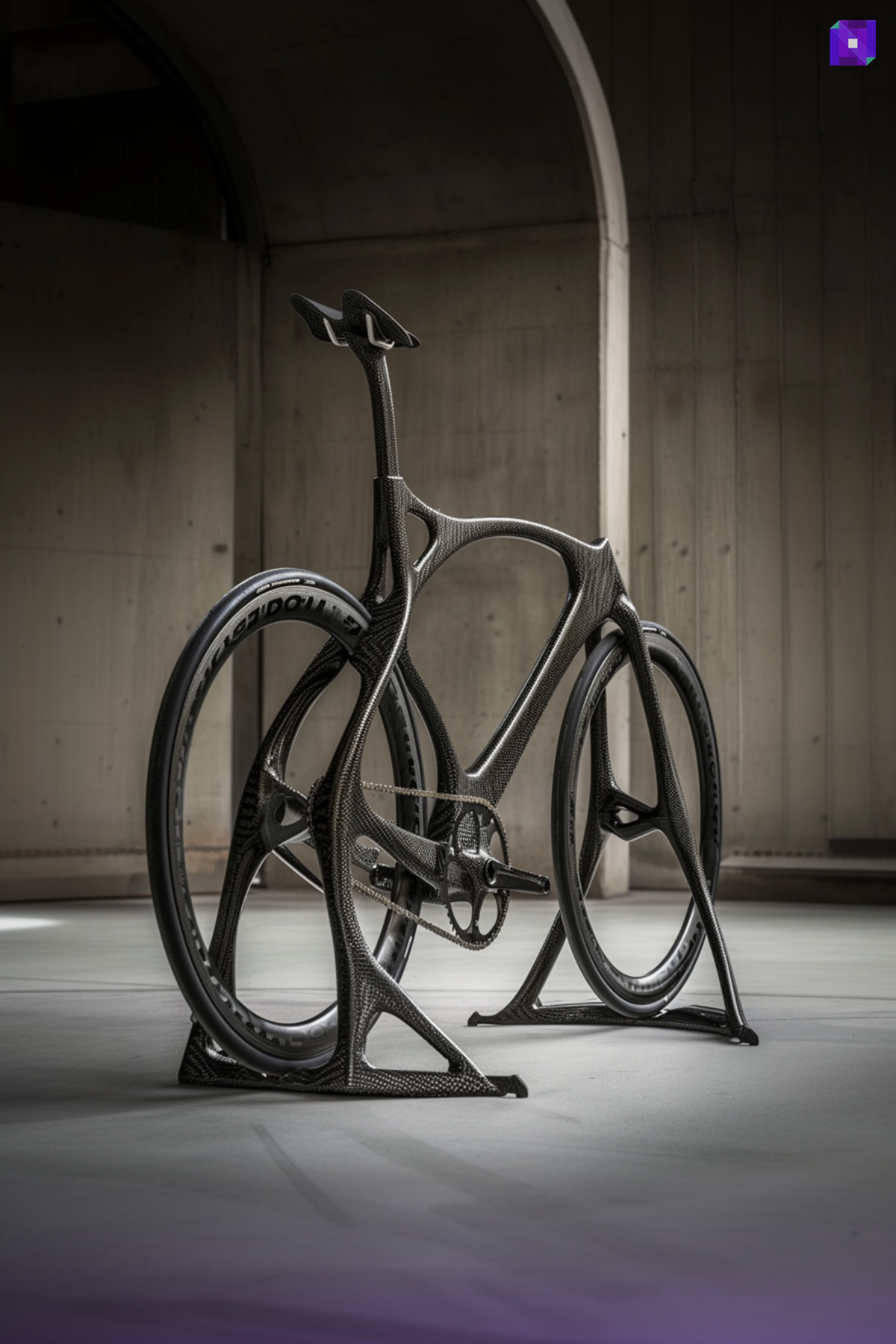
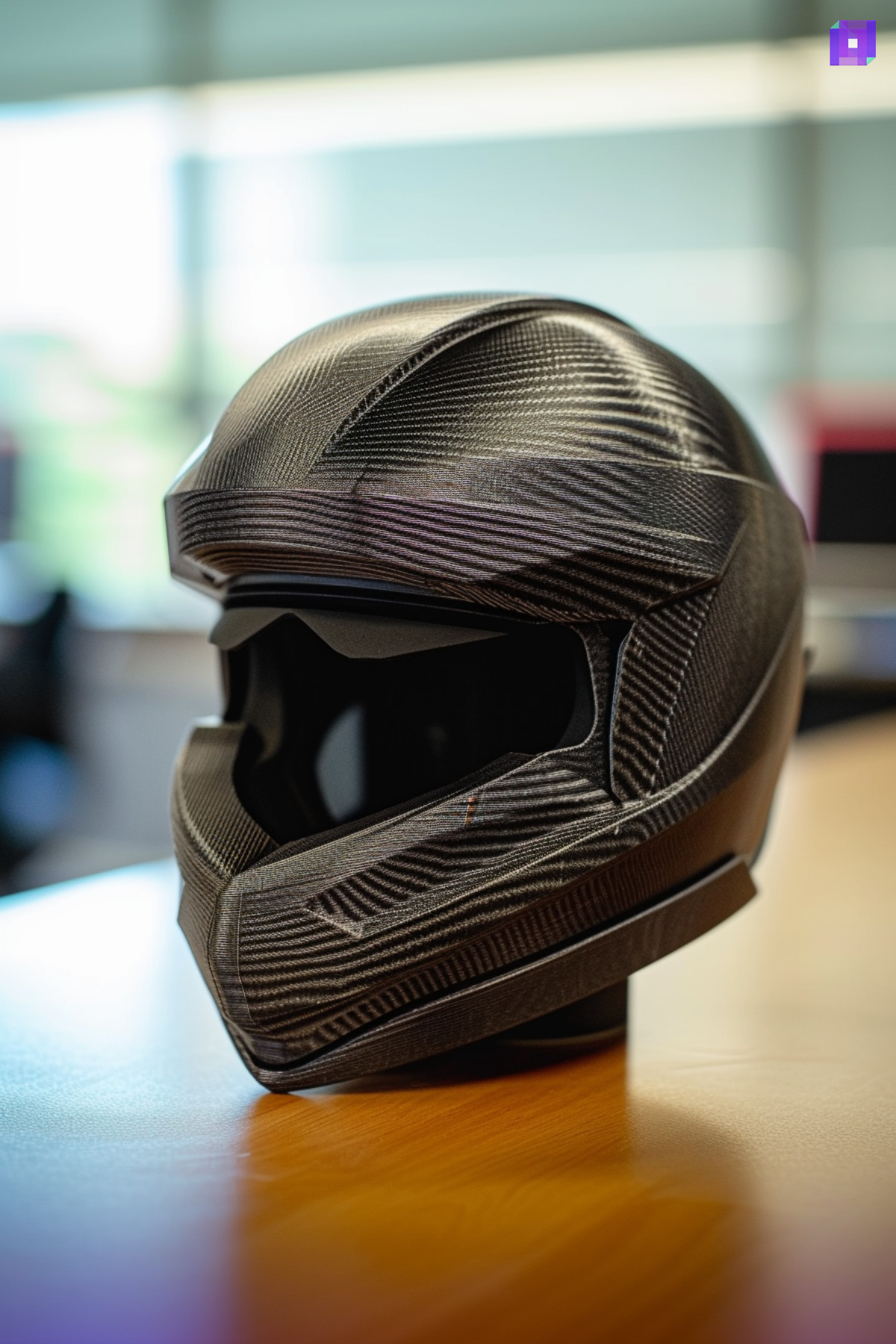
Ceramics
Have you ever wondered what makes your pottery so sturdy or how spaceships can withstand the intense heat of reentry? The answer, my friend, lies in the magic of ceramics! That’s right, ceramics aren’t just for delicate teacups. They are some of the most heat-resistant and biocompatible materials, making them perfect for things that feel the heat, like engines and turbines, not to mention life-saving biomedical implants.
Now, let’s talk about something cool — Zirconia. This tough cookie is often used in the binder jetting and laminated object manufacturing (LOM) methods of 3D printing. Imagine a material so hard and resistant to wear that it could easily be a superhero in the materials world. Thanks to these techniques, cutting tools, nozzles, and even armor are crafted from Zirconia. It’s like the Swiss Army knife of the ceramic family!
Additive Manufacturing Techniques | Examples Using Zirconia |
Binder Jetting | Cutting tools, Machine components |
Laminated Object Manufacturing (LOM) | Nozzles, Wear-resistant parts, Armor |
Let’s break it down a bit. Printing with ceramics mainly involves these things:
- Design Freedom: No more being shackled by traditional manufacturing limits! You can now design components with complex shapes that were once impossible or too expensive to make.
- Reduced Costs and Lead Times: Say goodbye to the need for pricey tooling and long waits! Producing those one-of-a-kind components just became faster and cheaper.
So there you have it, a quick dive into the world of ceramics in additive manufacturing.
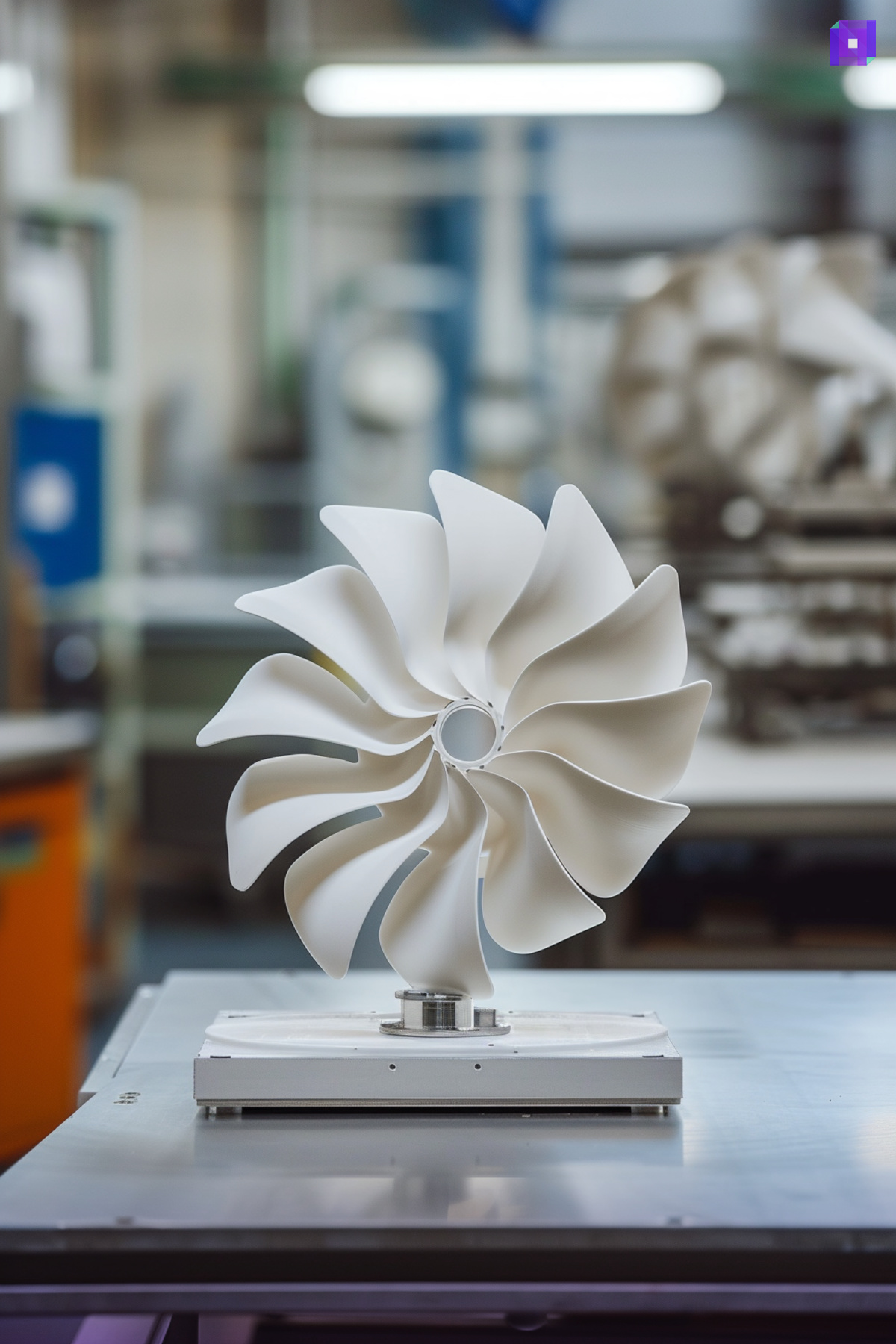
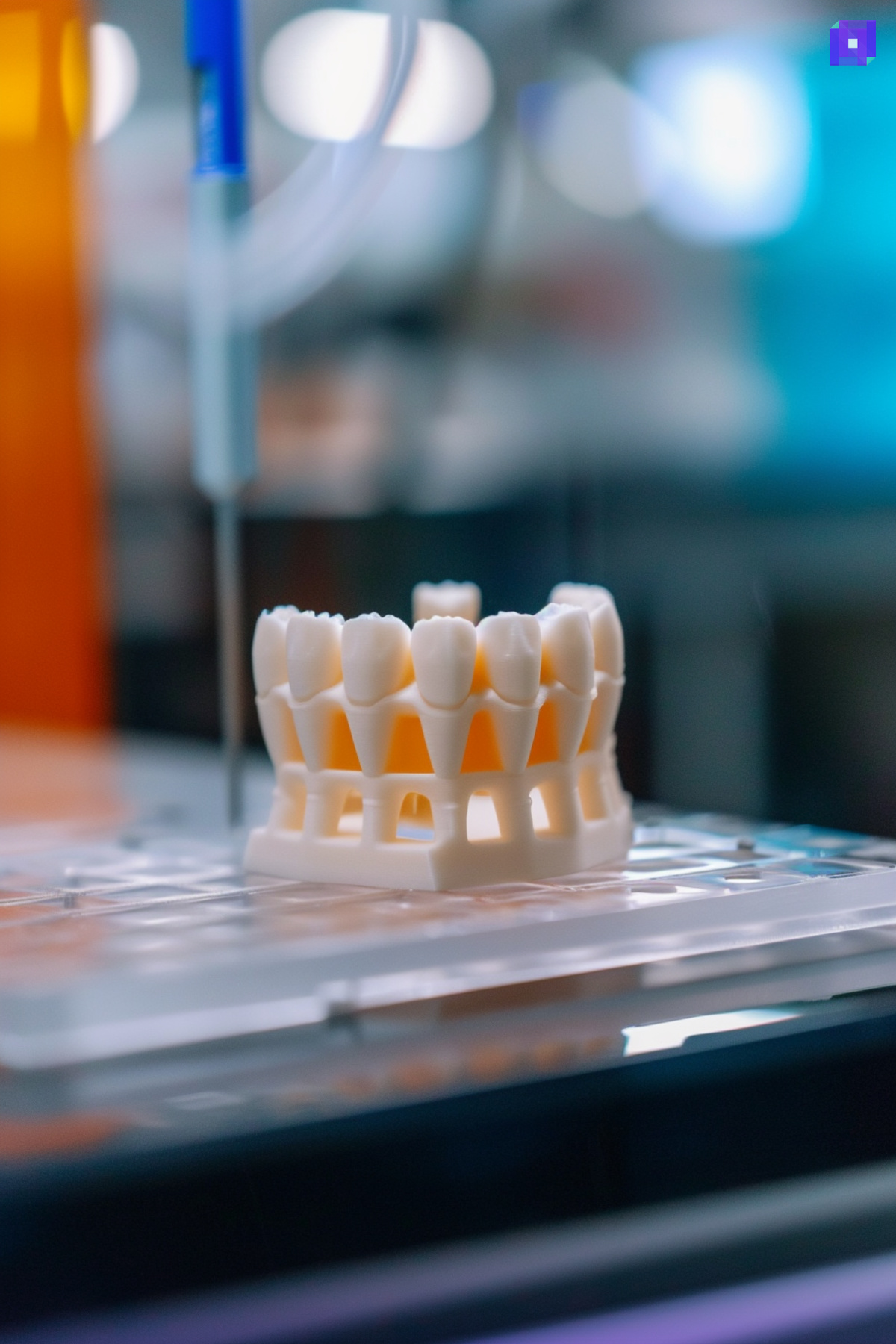
Biological
Have you ever imagined the far-reaching possibilities of creating living tissues with a printer? Well, it’s not science fiction anymore! In the dynamic field of AM, some of the most groundbreaking work involves biological materials. These materials range from living cells and tissues to DNA itself.
Imagine needing a skin graft after an injury. Instead of traditional methods, doctors can now use bioprinting to create an artificial version of your skin. That’s right, your skin! Bioprinting allows for the precise layering of bio-inks composed of cells and other biological matter, crafting structures like skin layers, blood vessels, or even more complex organs. For instance, researchers have made astounding progress printing grafts, heart valves, and even ears that can eventually integrate with your body!
Here’s how it could work for you:
- A 3D scan of the affected area ensures the bioprinted skin will be a perfect fit.
- Specialized printers lay down cells in the exact pattern to mimic natural skin.
- Over time, these cells grow and integrate with your body, just like biological tissue.
Using biological materials isn’t just innovative – it’s a game-changer in personalized medicine. Bones, cartilage, and even entire organs are on the horizon.
So, what does this mean for you? Potentially faster recovery times, reduced risk of rejection, and medical treatments tailored precisely to your needs. The future of medicine is being printed, offering hope and personalization in healthcare like never before.
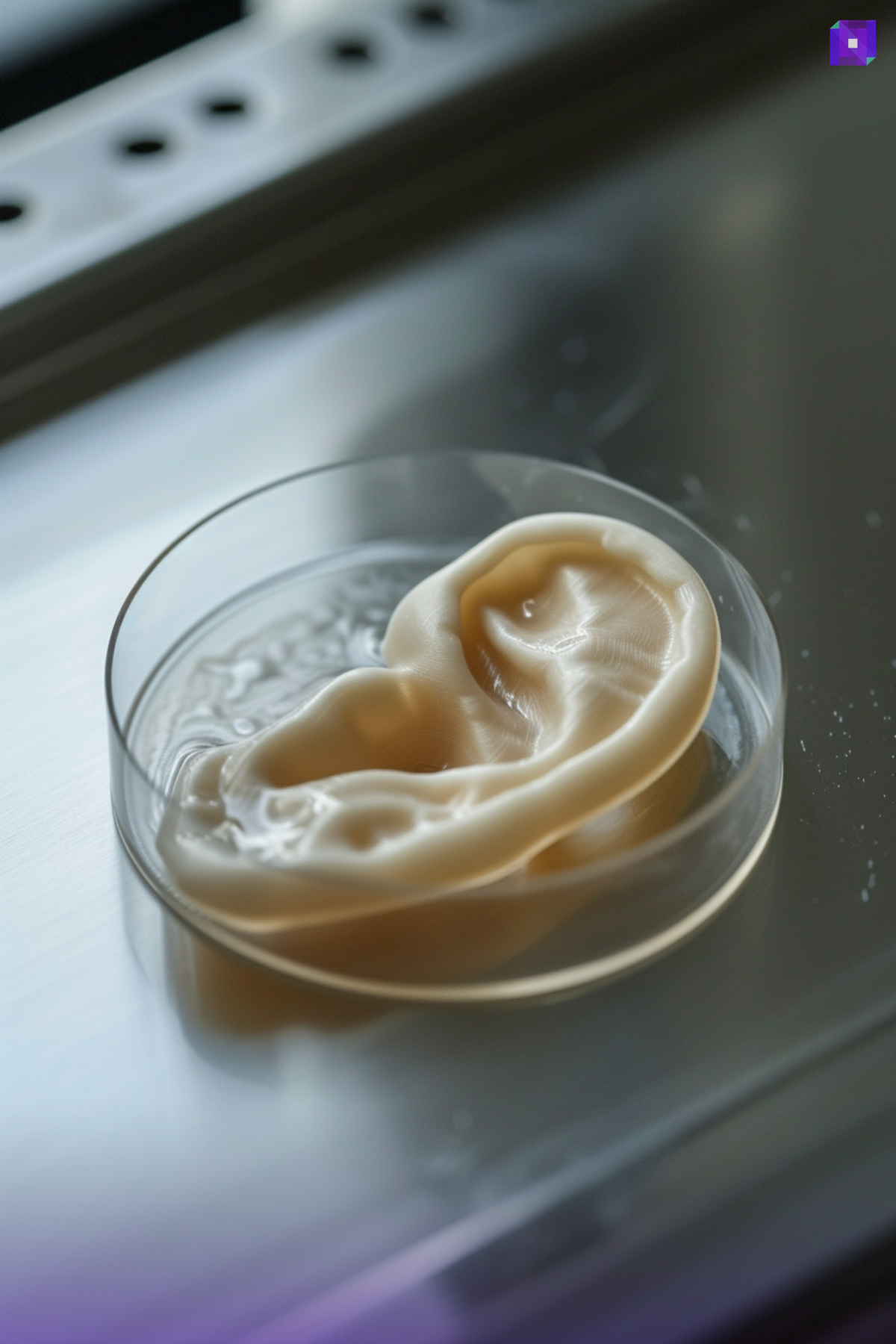
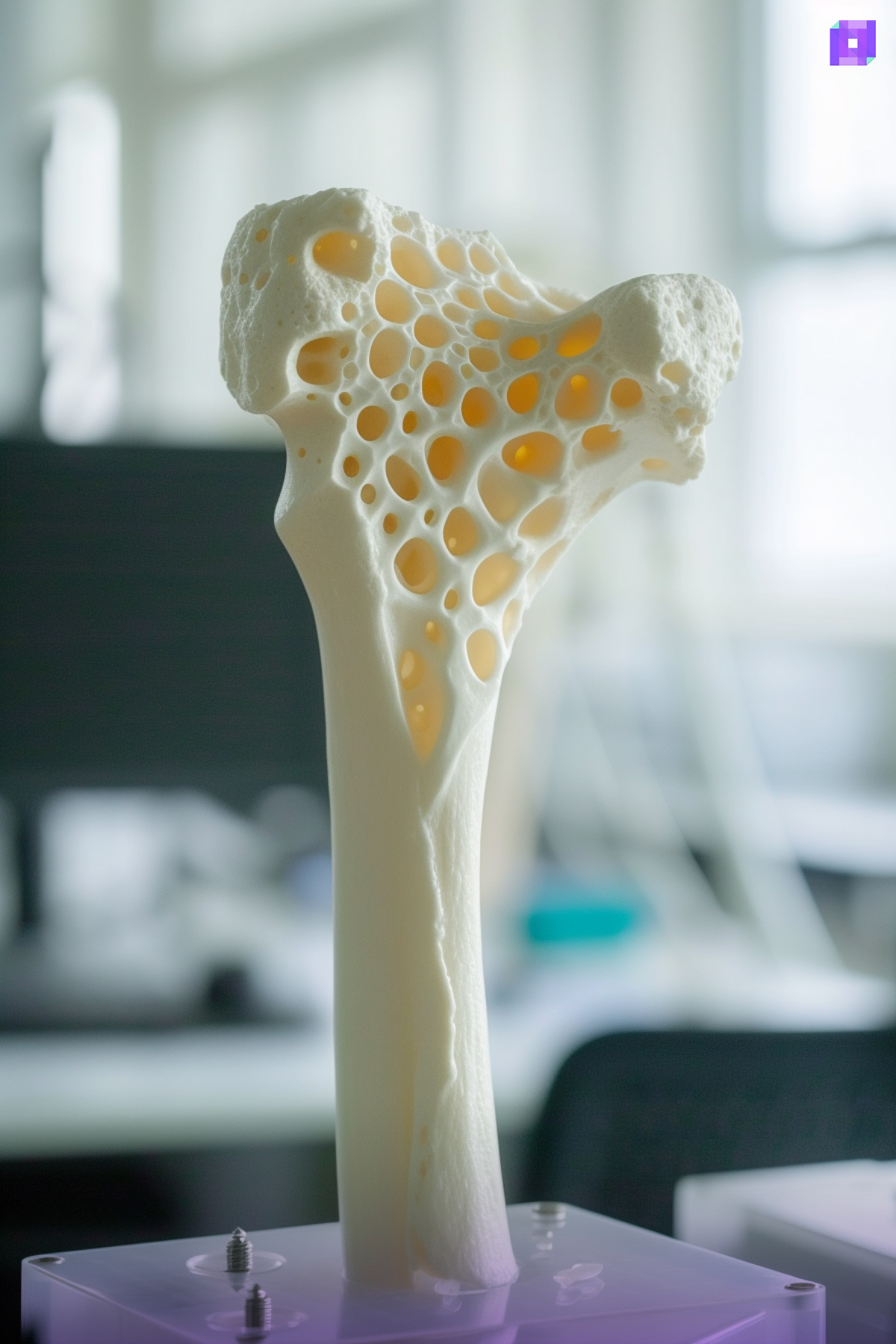
Other Materials
The broader selection of materials goes beyond the usual suspects of metals and thermoplastics!
For a little secret between us, there’s a whole world of gels, foams, and resins that are often the unsung heroes in this realm. Gels, for instance, have made a splash with their unique jelly-like consistency. They are perfect for applications requiring cushioning or soft-touch components. From comfy shoe insoles to squishy phone cases, gels have you covered!
Foams are another cool bunch. These airy materials bring lightweight properties and excellent thermal insulation, making them a choice for aerospace parts. Who wouldn’t want a featherlight yet strong material to keep everything cozy in space?
Now, onto the sticky stuff – resins. These viscous substances can be natural or synthetic magic potions that harden into solid plastic. Resins shine bright in stereo-lithography, built with a UV laser to form highly detailed and durable objects.
Here’s a quick glance at these materials:
- Gels: Think soft, flexible, and perfect for custom cushioning.
- Foams: Lightweight with thermal insulation. A favorite for the skies!
- Resins: The UV-light charmed substances turn liquid dreams into solid reality.
Each of these materials brings something unique and expands the horizon for what you can create.
Applications of Additive Manufacturing
AM has touched your life in ways you might not realize, changing how products are made across various industries. This technology’s capacity for creating complex geometries and providing design flexibility is beneficial in rapid prototyping, producing customized solutions, and advancing industrial production. Let’s look at how it is applied in various sectors.
In Healthcare
Is it surprising that the same technology used for your keychain trinkets is also revolutionizing the medical field? AM is vital in healthcare, allowing customized medical implants and prosthetics to be produced. These personalized products fit patients perfectly, improving comfort and functionality. Moreover, AM is pioneering the creation of living tissue, and even hearing aids are more comfortable and practical thanks to this precision technology.
In Aerospace
When it comes to flying high, there’s no room for error. The aerospace industry benefits immensely from AM, leveraging its ability to produce lightweight, complex geometries crucial for high-performance aerospace components. AM expedites the development of new aerospace designs and optimizes them for energy production and defense applications. Did you know that some of the components in scramjets and satellites are likely 3D printed?
In Automotive
Imagine a car tailored just for you, right down to its nuts and bolts. AM is accelerating the journey from concept to showroom in the automotive world. AM enables rapid prototyping and production of complex parts with intricate geometric shapes. The result? Lighter vehicles with improved fuel efficiency and performance. From a simple customization tweak to critical engine components, manufacturers use AM to drive innovation.
Beyond Traditional Industries
You might not be ready to eat a 3D-printed steak yet. Still, additive manufacturing is even making waves in the food industry. Chefs are experimenting with novel designs for dishes that were previously unimaginable. And it doesn’t stop there; additive technology is also constructing more sustainable houses and improving energy production systems with parts that might be too complex for traditional manufacturing methods. Wake up in a world where your home, your meal, and even the energy that powers them carry the mark of 3D printing.
Additive manufacturing is not just a tool; it’s a whole new playground across sectors, and its applications are limited only by our imagination.
The 7 Types of Additive Manufacturing
Let’s look at the seven fantastic types of AM that are reshaping industries left and right.
Powder Bed Fusion
Meet Powder Bed Fusion (PBF), your go-to additive manufacturing (AM) buddy that works wonders with powder and a heat source like a laser or electron beam.
How does it work? Imagine sprinkling a layer of powder, then zapping it precisely where you want it to melt and solidify—layer by layer—until you have a solid three-dimensional object.
Why choose PBF? Here’s what’s cool:
- Produces parts that are strong and dense.
- Enables complex designs that traditional methods can’t touch.
- It’s a champ at reducing waste because it uses only the material that ends up in your part.
But wait, it’s not all sunshine and rainbows:
- PBF calls for high heat and a controlled environment (think space-level conditions).
- It might leave you with stresses and distortions on your part—kind of a bummer but fixable.
- A little post-processing might be needed, which can be like giving your part a mini spa day.
What’s PBF good for? Got a medical or aerospace project? PBF could be your hero, crafting everything from implants to jet engine components.
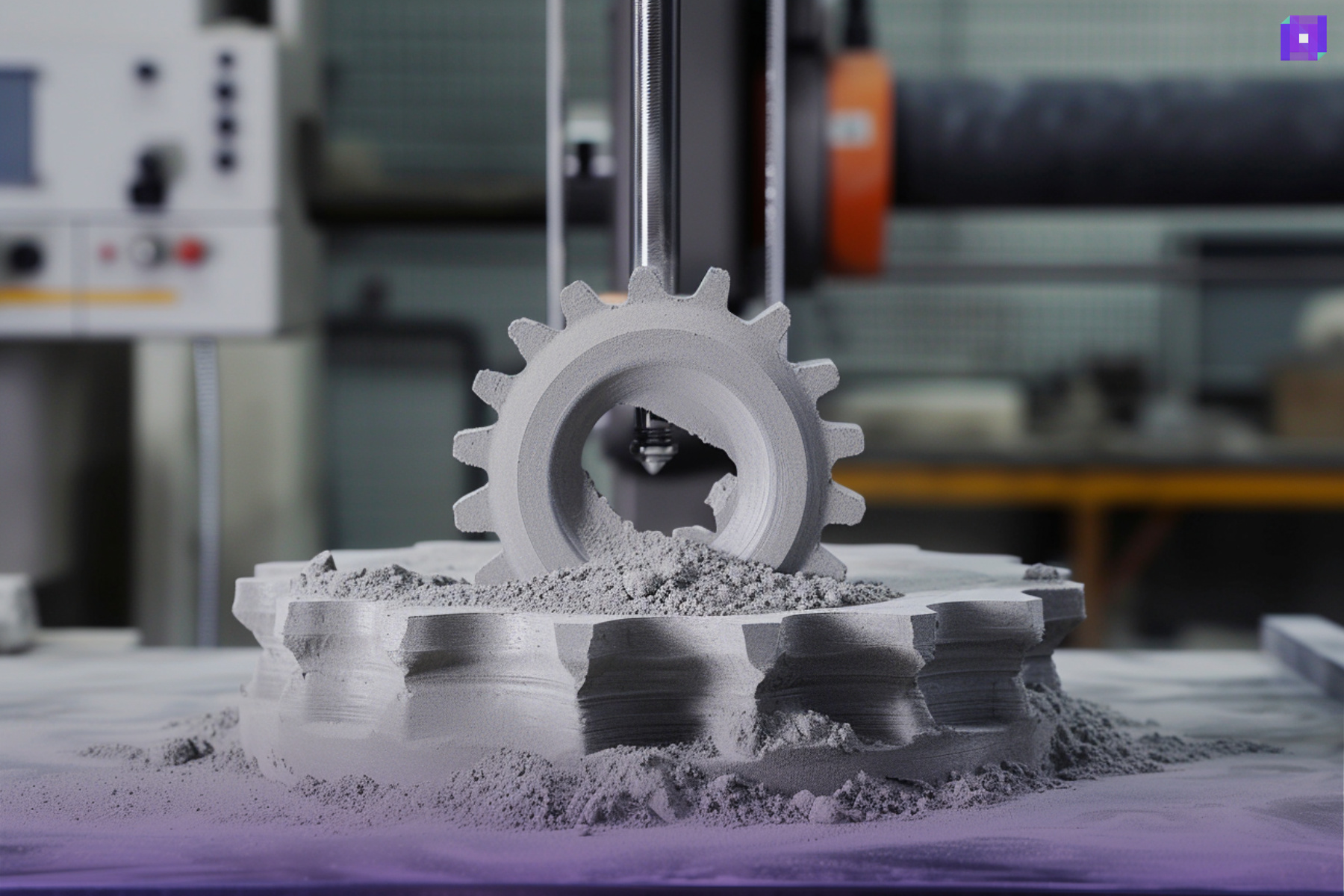
Directed Energy Deposition
Let’s demystify a fascinating technique, Directed Energy Deposition, or DED. Think of it like a high-tech glue gun, but it squirts molten or ceramic material through a nozzle onto a surface instead of glue.
How Does It Work?
- Nozzle: A precise delivery system for the material.
- Material: Metal or ceramic, often in powder or wire form.
- Heat Source: This could be a laser, arc, or electron beam that melts the material.
- Layering: Material is added layer by layer and solidifies upon deposition.
Now, imagine you’re printing in 3D but with an extra kick of thermal energy that fuses each layer as it goes. That’s DED for you – it’s like a high-stakes game of building blocks where you can mix different materials and create objects that might seem straight out of a sci-fi movie!
Why Use DED?
- Versatility: It loves to play with various materials, creating unique gradients and multi-material structures.
- Size Matters: It quickly goes big, crafting large-scale parts that other methods might struggle with.
- Repairs & Additions: Breathe new life into damaged parts or add features to existing components.
However, DED could be better. It’s rough around the edges. The surfaces it creates can be gritty, and the microscopic structure might not be as refined as other methods. But if you’re into function over form, these quirks will only bug you a little.
Practical Uses
- In the Air: It’s a hit in aerospace for repairing turbine blades.
- At Sea: Naval sectors use it to fix ship components without starting from scratch.
- Creativity Unleashed: Artists and designers exploit its prowess to fabricate intricate, layered sculptures.
DED truly shines when you need a custom job or a quick fix. While it’s not about to stitch up your jeans, it’s definitely the go-to for keeping your high-tech gear in top shape.
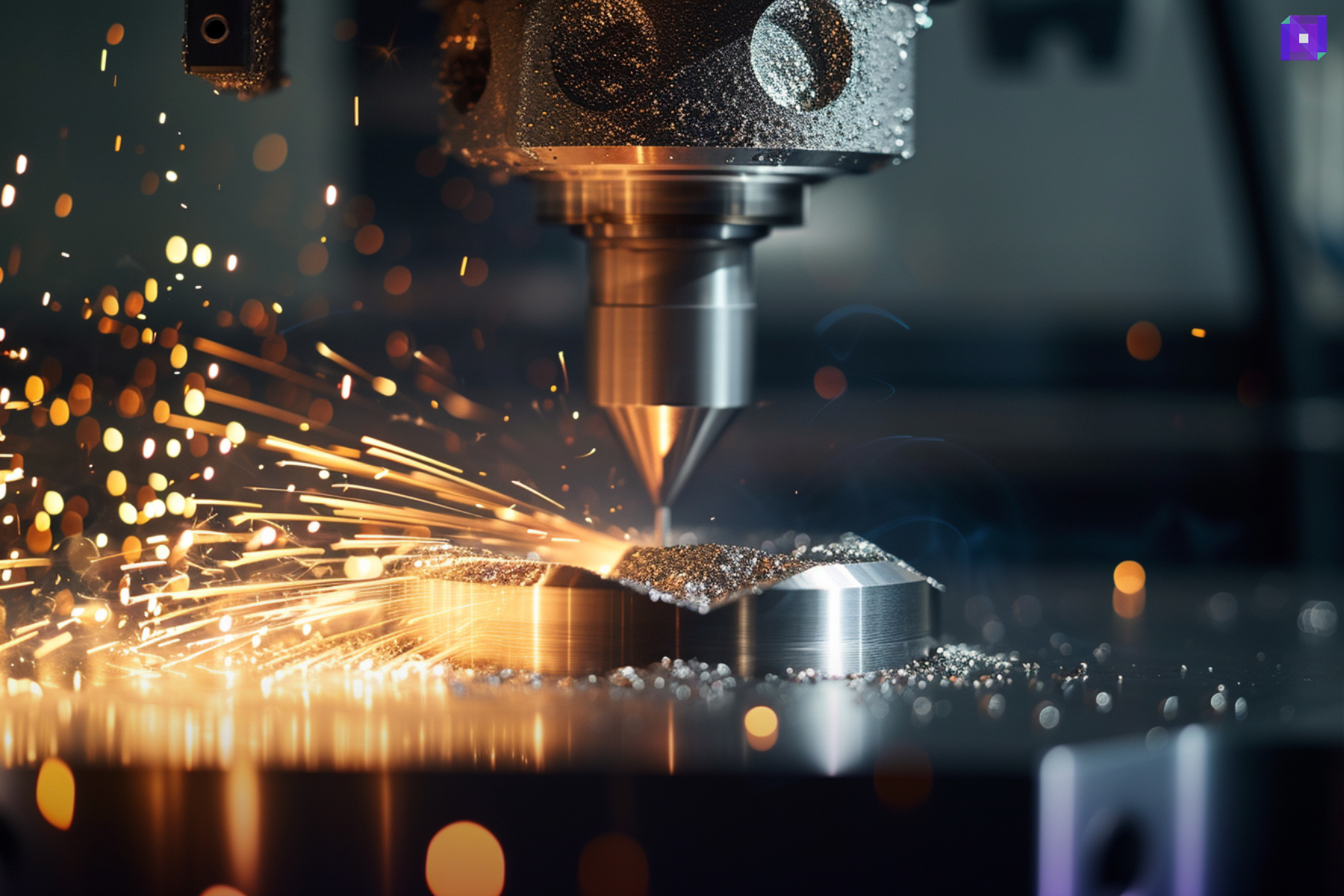
Binder Jetting
Binder Jetting is your ticket to watching engineering magic unfold. Yes, it’s a futuristic technique that’s like printing your paper documents, except you’re crafting a real, tangible object.
Here’s the scoop: a print head zips across a bed of powder, precisely shooting out a liquid binder. Picture it as sprinkling fairy dust that makes the powder stick together, layer by glorious layer, building your object from the ground up.
Why it’s cool:
- Full-color capabilities: It’s like having a crayon box with endless colors for your prints.
- Material freedom: Metals, sand, ceramics – choose your playground.
- Spongy surprise: High porosity means these parts can be lightweight yet nifty.
But wait, there’s more:
- Post-processing: Just because the printer stops doesn’t mean you’re done. Some spa-like sintering or a dash of infiltration might be in order.
- Strength and precision: They’re not quite superheroes. Sensitivity to the elements and a gentler touch in strength and accuracy can be kryptonite.
Curious about what it can make? How about intricate gears for your gadgets or molds for manufacturers? There are plenty of possibilities with Binder Jetting.
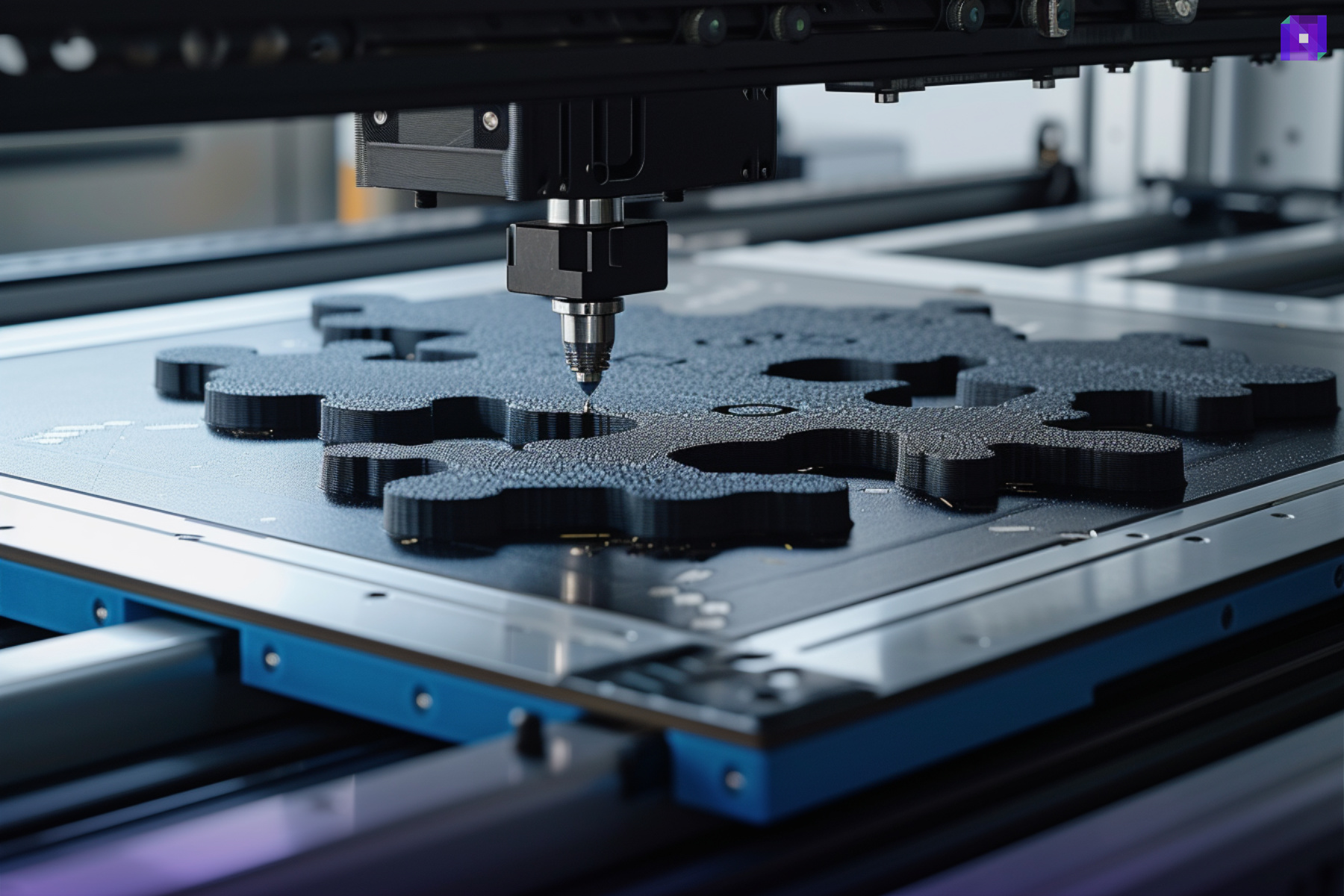
Sheet Lamination
Sheet lamination is a friendly member of the additive manufacturing (AM) family with some tricks up its sleeve. Here’s the scoop: you stack and bond layers upon sheet material layers— paper, plastic, or even metal—to craft a solid object.
Are you in a hurry but want to maintain quality? Sheet lamination might be your go-to process. Why? It’s fast and cost-effective, thank goodness! Plus, it uses materials that are easy to find. No need to hunt for exotic components.
Benefits:
- Quick prototyping
- Economical with off-the-shelf materials
- Stronger and stiffer parts
But hey, nobody’s perfect, right? While sheet lamination is doing its best, it does have a few drawbacks:
- Visible layer lines (beauty is not skin deep, after all)
- Fewer material options
- The surface finish might need a makeup touch-up (think post-processing)
So, what can you actually make with sheet lamination? I’m glad you asked!
Examples:
- Architectural models that make you look pro
- Educational tools (yes, learning can be fun!)
- Components that play well with others in assemblies
Remember, you’re aiming for something robust and practical, even if it’s not winning beauty pageants. And, if you’re okay with a few extra steps of post-process pampering, you’ll get rid of those pesky layer lines and get surfaces smooth enough to slide on.
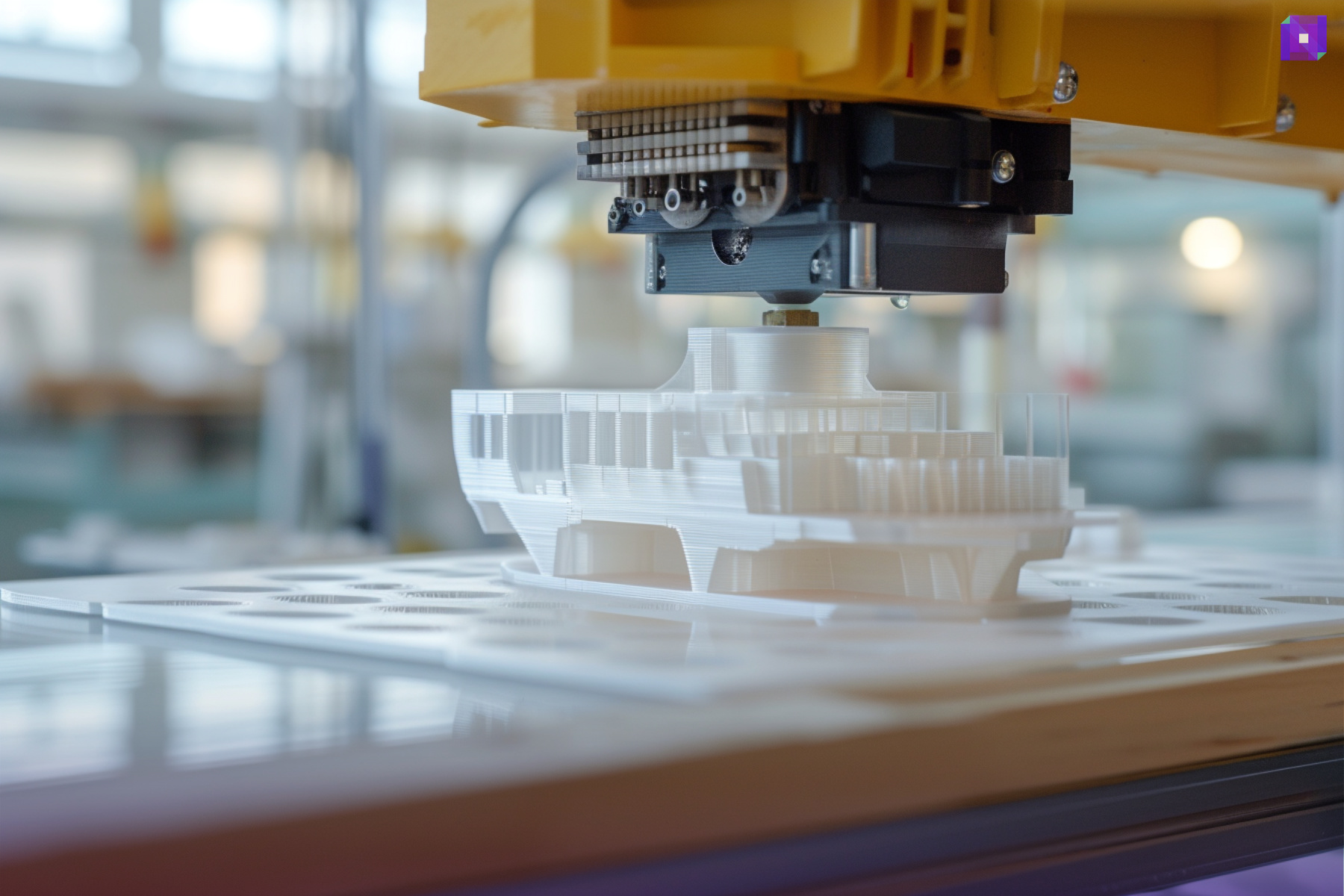
Material Extrusion
Material extrusion involves squeezing a material—like plastics, metals, or concrete—through a nozzle onto a build platform. As you’d ice a cake, this material is applied layer by layer, hardening to form a finalized 3D object.
Pros of Material Extrusion:
- Simplicity: It’s straightforward to use. You don’t need a PhD to get it up and running!
- Cost-Effectiveness: Generally more affordable compared to other AM techniques.
- Material Diversity: Works with various materials, from standard plastics to innovative composites.
- Structural Integrity: Produces parts with good layer adhesion, enhancing stability.
Cons of Material Extrusion:
- Resolution and Accuracy: Not quite the method for intricate details.
- Warping/Cracking: It’s not unheard of to have a part relaxed unevenly and decide to twist out of shape.
- Post-Processing Necessities: Supports to prop up overhangs and additional smoothing might be needed.
Now, you might wonder, “What sort of stuff can you make with this?” From prototypes to functional household items, material extrusion has got you covered. It’s also making waves in the medical field for creating custom prosthetics – talk about sci-fi becoming reality!
Remember, this 3D printing sibling isn’t perfect; no actual sibling is! It might test your patience with its support structures and post-processing needs. But despite the downsides, material extrusion stands as a go-to for hobbyists and industries alike, offering a balance between user-friendliness and practical performance.
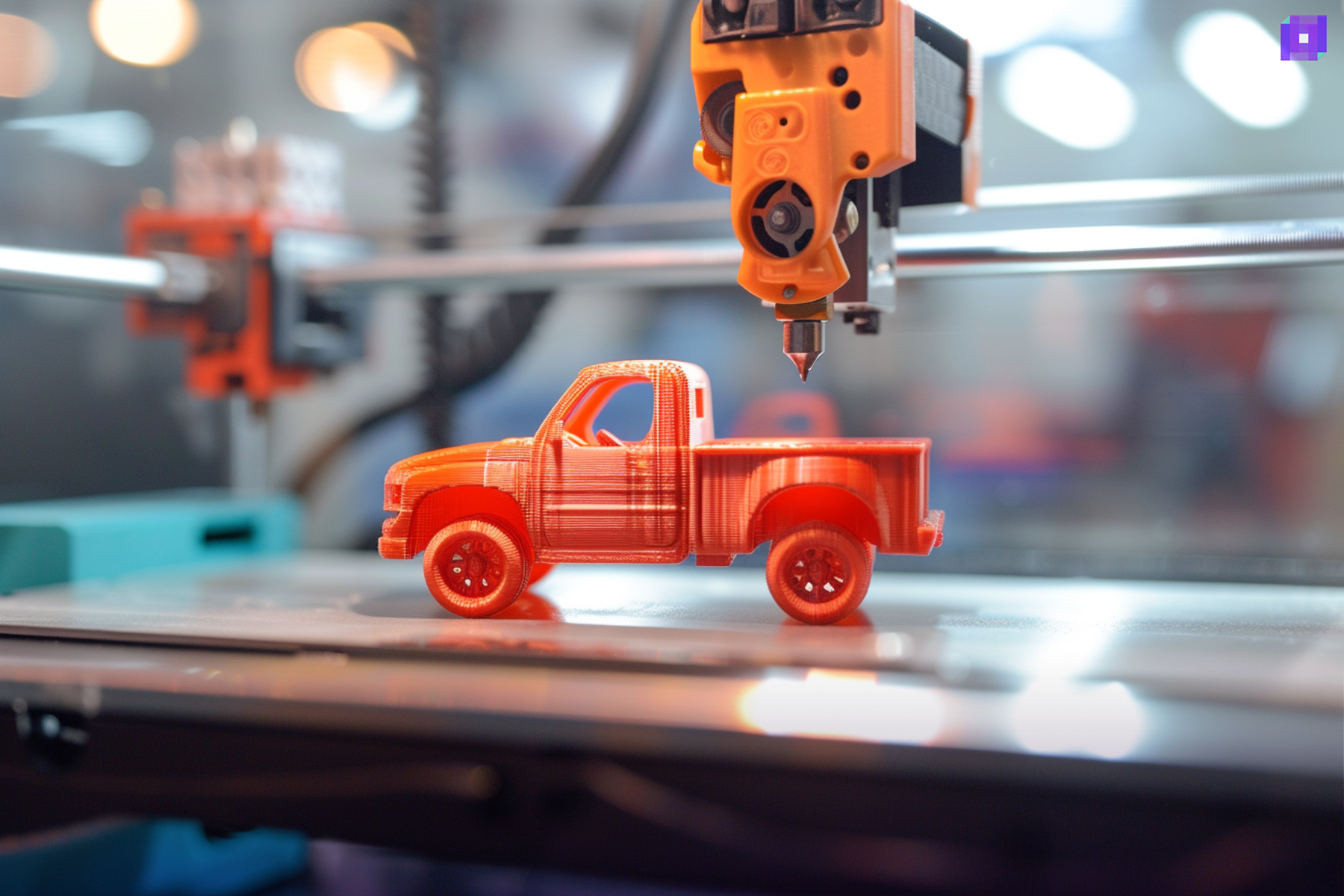
Material Jetting
Picture a print head, quite like the one in your inkjet printer, but instead of ink, it squirts out tiny droplets of material—that could be a rigid plastic, a precious metal, or even wax—onto a platform below, layer by dainty layer.
Why should you care? Well, Material Jetting is like the fine artist of the 3D printing world, crafting parts with such high-resolution and silky-smooth surfaces that you’d want to reach out and touch them. It’s the go-to for products that need a show-worthy finish straight out of the printer. And guess what? You can get your model in living color because this technology adores full-color printing. Multi-material printing? No problem!
While it might sound like your 3D dreams come true, remember that everything has its trade-offs. Think of Material Jetting as a high-maintenance friend. It’s on the pricey side and likes to take things slow and carefully, requiring support structures and a bit of time in the curing spa to harden correctly. Plus, don’t expect it to hold up like a superhero; it’s more the delicate type, with lower mechanical strength and less durability than other AM siblings.
Before you wander off, let me paint you a picture of what Material Jetting can whip up:
- Intricate jewelry that captures every minute detail
- Detailed architectural models showcasing textures and gradients
- Customized medical devices tailored to be as unique as you are
If you’re in the market for something that looks sleek, feels smooth, and screams quality (without worrying too much about the cost), Material Jetting might be your perfect match in the 3D printing world.
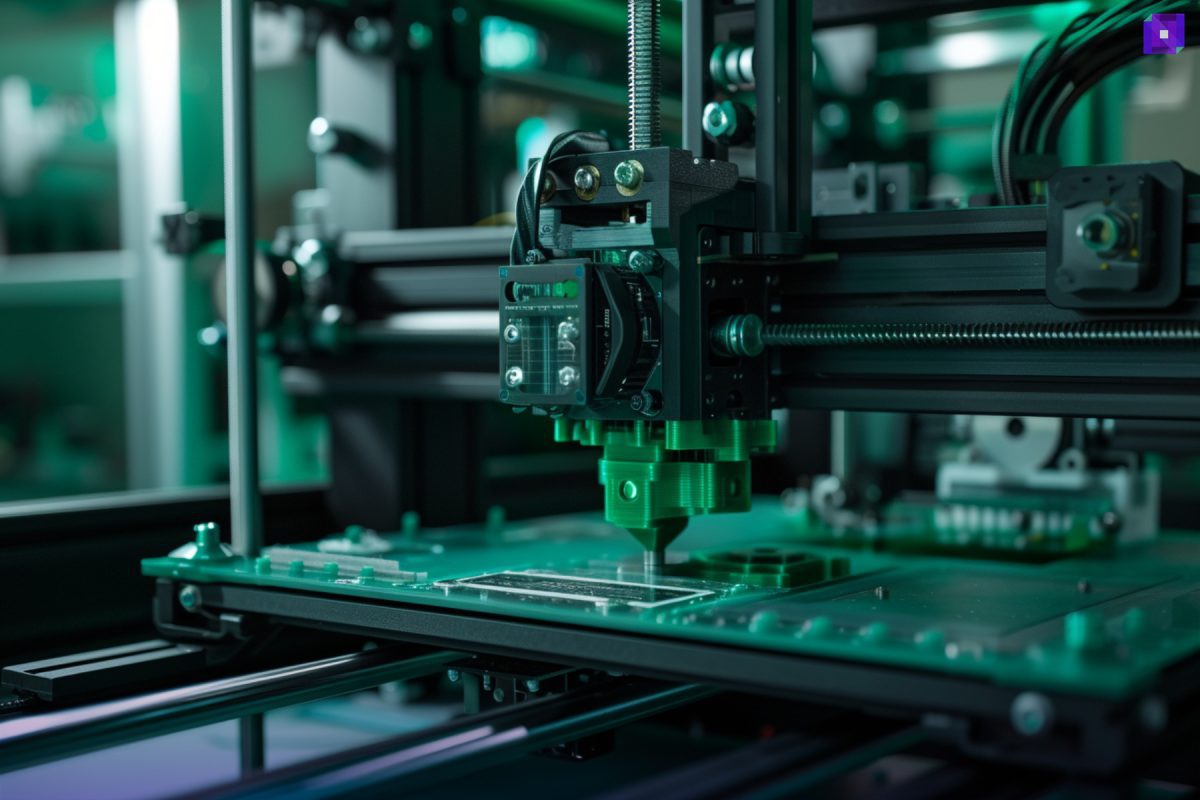
VAT Photo-polymerization
Imagine you’re painting with light; that’s how vat photo-polymerization works. Using a light source such as a laser, projector, or LED brings to life 3D objects by curing a liquid photopolymer resin.
Pros:
- High-resolution outputs? Check.
- Surfaces as smooth as jazz? Absolutely.
- Dreaming of complex geometries and fine details? No problem.
- The variety of resins available lets you pick the perfect one for your project.
Cons:
- It can hit your wallet, as it’s pricier.
- Handling the resins requires care—they can be hazardous.
- Think of scaffolding, but for printing—supports are a must and don’t forget the post-curing.
- It may not be the Hulk of materials, with some printed objects having lower mechanical strength and stability.
Applications | Products |
Biomedical | Custom Dental Implants |
Functional Devices | Prototype Engine Parts |
Ceramics | Artistic Sculptures |
Tips: If you want to use VAT photo-polymerization, remember to handle the materials carefully and support your structures well during printing.
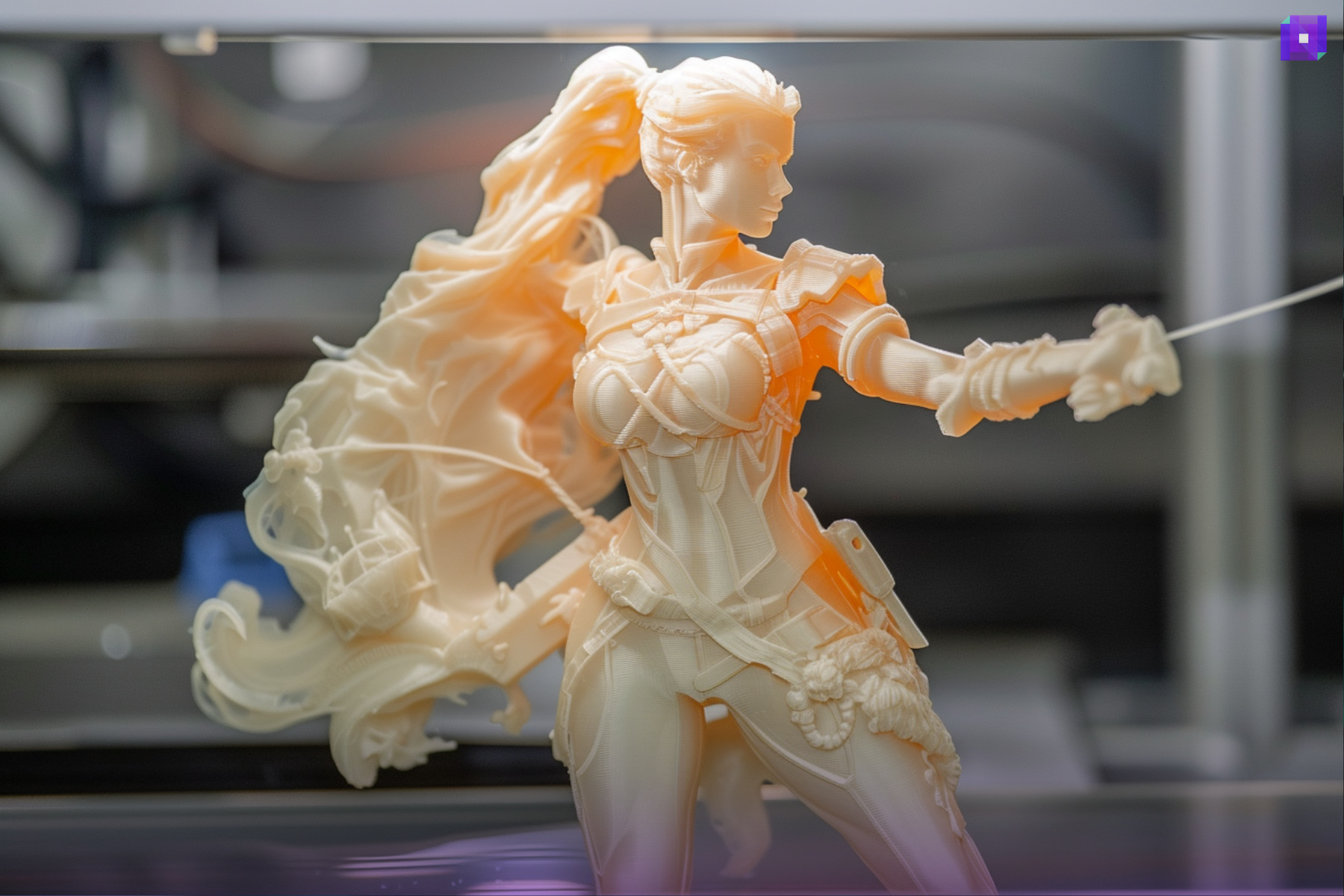
Advantages and Challenges of Additive Manufacturing
While we often hear about 3D printing, there’s more to AM than just a trendy buzzword—it’s full of perks but, like any technology, has its drawbacks. Let’s sift through them together.
Advantages
- Customization: Whether it’s a bespoke piece of jewelry or a specialized medical implant, AM caters to your unique needs. No design is too complex; no idea is too out-of-the-box!
- Complex Geometries: Imagine intricate latticework in lightweight aerospace components. Think of the most complex structure you can; AM turns it into reality, often with mind-boggling precision.
- Material Savings: Traditional methods can be wasteful, but AM is like a meticulous chef – it only uses what it needs, minimizing scrap and maximizing material use.
- Cost Reduction: Now, let’s talk dollars and sense. With no need for costly molds or tooling and the ability to print on demand, AM cuts costs across the board.
- Lead Times: Need something yesterday? AM accelerates product development. Say goodbye to long lead times and hello to rapid prototyping.
Benefits | How AM Makes It Happen |
Speed & Efficiency | Cuts out tooling and inventory, boosts on-demand production |
Complex Designs | Crafts parts with curved channels and hollow sections |
Small Batches | Offers mass customization without the mass production costs |
But wait, there’s more! AM isn’t just about saving money; it’s also a sustainability champion. And when it comes to innovation, the sky’s the limit – we’re talking parts with different properties all in one.
Challenges
Despite its promise, AM still has its fair share of head-scratchers. Let’s unpack a few.
Costs—They’re Hefty! Imagine investing in the latest AM machine—ouch, right? The advanced technology packs a punch to your wallet, including ongoing maintenance. But remember, great tech isn’t cheap!
- Material Mayhem: Have you ever had a print that didn’t turn out right? You’re not alone. Achieving that perfect print can be tricky when defects like porosity and cracks sneak in. It’s a dance of getting material qualities while the printer does its layer-by-layer magic.
- Mechanical Mysteries: AM parts, much like detectives, could use some post-processing to uncover their true potential. Think cleaning, curing, and even a polish here and there to achieve that ideal mechanical property or precision finish.
- Post-Processing Puzzles: After the printing party ends, the real work begins. It’s time to get down to the nitty-gritty with operations that refine those AM parts to perfection.
- The Waste Woes: No one likes waste, and AM tries its best to keep it minimal. However, some waste is inevitable, whether it’s support materials or failed prints. It’s all about finding ways to reduce, reuse, and recycle.
- Precision Perfection: Seeking immaculate print precision can be like chasing a mirage. It’s possible, sure, but it demands consistency and attention to detail every step of the way.
While these challenges might have you scratching your head, don’t fret too much. With each stumbling block comes a stepping stone, and where there’s a will (and continuous innovation), there’s a way!
Frequently Asked Questions
In this section, we’ve compiled a set of FAQs to give you a quick look at the essentials of additive manufacturing, including how it differs from traditional processes, the materials used, key industry players, and its unique benefits. Let’s dive right into your questions!
Additive manufacturing builds objects layer by layer from a digital file, often using computer-aided design (CAD) software, whereas traditional manufacturing typically starts with a bulk material that is subsequently cut down to shape the final product. This means additive processes can reduce material waste and allow for more complex geometries.
Common materials include plastics, metals, and ceramics. The material choice affects the product’s properties: plastics are versatile and lightweight, metals are strong and durable, and ceramics can withstand high temperatures. Each material opens unique possibilities for the design and application of the final object.
Companies leading the way include Stratasys, 3D Systems, and EOS. These companies have contributed to significant technological advancements, expanding their applications across various industries.
This technology is part of a suite of advanced manufacturing technologies that increase automation, improve precision, and offer customization. It’s often used alongside subtractive methods (like CNC machining) and complementary technologies like the Internet of Things (IoT) and artificial intelligence (AI) to optimize production.
Unique advantages include its ability to create complex, lightweight structures, reduce material waste, and provide customization at no extra cost. It also enables rapid prototyping, accelerating the design process and bringing products to market faster.
It is most prevalent in industries like aerospace, automotive, and healthcare. For the future, this translates to an increase in on-demand production, supply chain flexibility, and innovation in product design and material science. As these applications grow, production could become more localized and customized.